Efficiency is the golden word in the realm of industrial operations. A well-run industrial plant not only maintains productivity but also ensures environmental responsibility, worker safety, and cost efficiency.
To achieve this, several pieces must fall into place, from state-of-the-art machinery to meticulous maintenance schedules. Ensuring all these aspects work in harmony is crucial for a plant’s success. In this article, we explore the pivotal elements that contribute to an efficient industrial plant operation.
Essential Components for High-Performance Industrial Operations
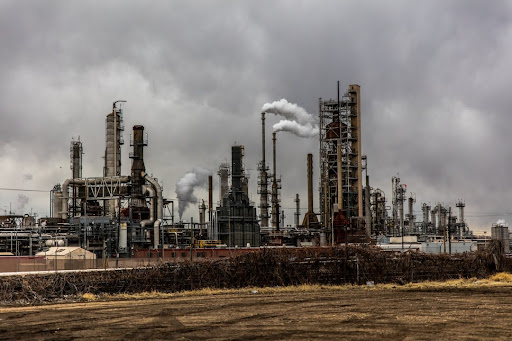
In today’s competitive marketplace, high-performing industrial components are essential. Machinery must withstand heavy use and adapt quickly to production demands. Integrated systems and software, such as network monitoring tools, are crucial for maintaining smooth operations and alerting managers to potential issues before they cause downtime.
Equally important is a skilled workforce. Continuous education and training keep personnel current with the latest operational standards and technological advancements, directly impacting product quality and plant efficiency.
A reliable supply chain is critical for timely and cost-effective delivery of raw materials, minimizing production halts and improving inventory management. A strong logistics framework ensures the steady flow of finished products to the market.
Data analysis tools are increasingly vital for identifying patterns, predicting maintenance needs, and optimizing resource allocation. These smart systems process large amounts of information to provide actionable insights, enhancing decision-making and productivity.
Streamlining Workflow with Advanced Manufacturing Technologies
Embracing modern manufacturing technologies streamlines workflows by increasing production speeds and reducing human error. Automation and robotics perform dangerous or labor-intensive tasks, enhancing worker safety.
Digital twins and simulations optimize processes without disrupting production. By creating virtual replicas, plants can test changes, forecast outcomes, and identify improvements without real-world risks.
Additive manufacturing, or 3D printing, has transformed prototyping and small-scale production. It speeds up new design launches and allows for greater customization, helping plants cater to niche markets and swiftly adapt to consumer demands.
IoT devices enhance connectivity and intelligence on the plant floor. They collect and transmit real-time data, enabling machine communication and allowing managers to monitor workflows remotely.
Effective Energy Management Strategies in Industrial Settings
In today’s era of environmental awareness and rising energy prices, effective energy management is essential. Accurate monitoring of energy consumption across plant processes minimizes waste, cuts costs, and supports sustainable practices.
Investing in renewable energy sources like solar and wind can reduce industrial dependence on fossil fuels and lower carbon footprints. For example, a fuel supplier in Saskatchewan can provide sustainable fuel options tailored to local industrial needs.
Upgrading to energy-efficient equipment, such as LED lighting, high-efficiency motors, and smart HVAC systems, significantly reduces energy usage. Regular energy audits are crucial for identifying areas to cut energy use. These audits can suggest operational changes that lower energy expenditure without compromising output.
Prioritizing Safety and Compliance in Industrial Environments
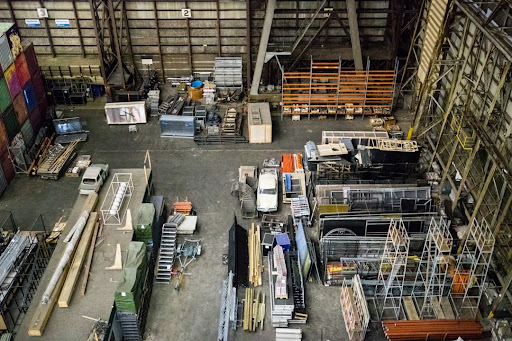
Industrial safety and compliance are crucial for maintaining operational integrity. Following industry regulations protects employees, the environment, and the community while preventing legal and financial issues due to non-compliance.
Investing in modern safety equipment, such as alarms, fire suppression systems, and personal protective gear, is essential. Continuous safety training and clear procedural communication foster a safety culture that goes beyond compliance.
Audit trails and documentation are vital for compliance. Detailed records of safety checks, incident reports, and corrective actions create a transparent trail useful during inspections or accidents.
Risk assessments and proactive measures are necessary to anticipate and mitigate hazards. Regularly updating safety protocols ensures their effectiveness and relevance amid changing circumstances or new threats.
Implementing Continuous Improvement Practices for Plant Optimization
Continuous improvement practices like Six Sigma and Lean Manufacturing optimize industrial processes through systematic refinement. These methodologies focus on ongoing enhancements, targeting even minor efficiencies for overall improvement.
Establishing and tracking key performance indicators (KPIs) is crucial to measure the effectiveness of continuous improvement efforts. Metrics such as cycle time reduction, cost savings, and customer satisfaction provide objective data, guiding targeted strategies for enhancement.
Employee engagement is vital in continuous improvement. When the entire workforce participates in suggesting and implementing improvements, it fosters a culture that values innovation and practical problem-solving.
Pilot programs and small-scale tests are essential for evaluating the impact of proposed changes. These trials allow for fine-tuning and iteration, reducing risk and leading to successful full-scale rollouts of new processes or technologies.
Altogether, running an efficient industrial plant relies on a balance of technology, human resources, safety, and continuous improvement. Managing these elements diligently ensures high performance, compliance, and competitiveness. Integration of innovative tech, sustainable practices, and a dedicated workforce drives efficiency, safety, and prosperity.